Automotive
The History and Anatomy of Drum Brake Systems
Drum brakes are a type of braking system for vehicles that use drums to slow the wheels when stopping. They are usually found on trucks, buses, and cars from the 1960s until today. They were designed to be more effective than traditional braking systems which rely on only the front brakes, by using rear brake wheel drums to create a dynamic friction zone that will provide increased stopping power. This is accomplished by putting pressure on the fluid inside the drum through a piston connected to the wheel. When the piston is pushed in, the fluid is forced out against the brake pad, creating more friction and stopping power.
History of Drum Brakes
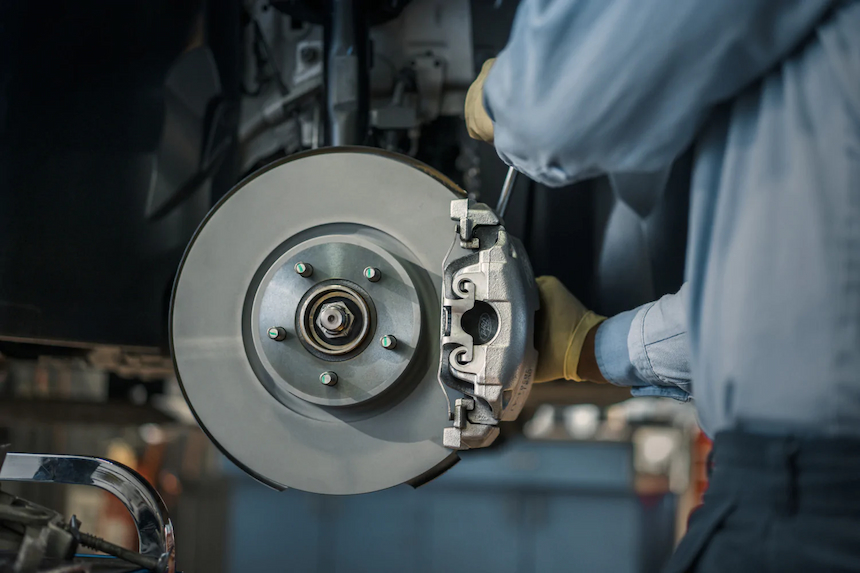
source: ford.co.uk
The first drum brake was invented by Louis Bouquet, a French engineer working for Sanguinetti et Cie, in 1868. He created it as a replacement for front wheel brakes which had been used on trains since 1830 but were not effective in stopping horse-drawn carriages because they only applied pressure to one of the rear wheels.
His invention consisted of two metal pads attached to springs that were mounted behind the front wheels. When engaged, the springs would pull both pads inwards causing friction with the ground and stopping the vehicle. Bouquet’s invention was not patented or mass-produced; however, it did lead to other improvements such as a better spring for vehicles and brakes for railway trains.
The first drum brake to be patented was by American George Westinghouse in 1871. His design used two sets of shoes that could be moved closer together or farther apart using a control lever on the handlebars. This allowed the rider to select how much braking force was needed. The shoes were connected to a metal cylinder with friction material inside it, which pulled against brake wheel drums when pressure was applied.
Westinghouse’s invention was created as an improvement on existing braking systems and he stated that it would be “extremely valuable for stopping street cars”. Shortly after its creation, this new type of brake was installed on some Pullman trains at the Pennsylvania Railroad (PRR).
In 1874, Englishman William Leaver patented a similar design that used a lever to control the pressure on both sides of the drum at once. He also modified it so that one shoe could be moved closer than the other, giving more stopping power on one side of the vehicle or allowing it to swerve around objects without having to brake as much.
The first drum brakes were installed on horse-drawn carriages and were only meant to slow them down. By 1900 they had been adapted for use on automobiles and were being installed on the rear wheels. They became popular with automakers because they could be used to slow down while still allowing the vehicle to be moved from one side of a road to another. These brakes also provided more stopping power than traditional systems which only had front brakes, since they used both rear wheels.
Drum brakes were widely used in the 1960s and 1970s on trucks and buses. They are still used today on some trucks and commercial vehicles; however, they have mostly been replaced by disc brakes which are more effective and less expensive to maintain.
Anatomy of Drum Brakes
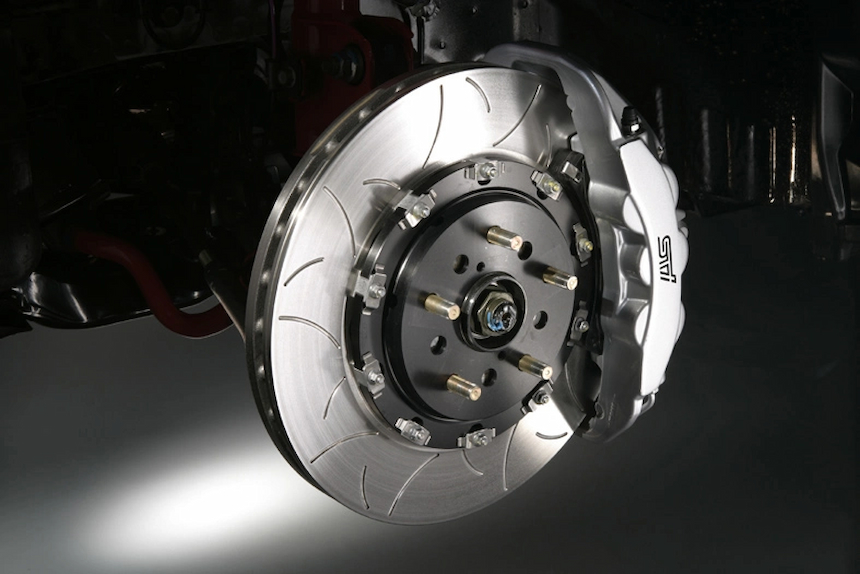
source: fjreviews.wordpress.com
The main component of a drum brake is the drum itself, which provides housing for all other parts. It is usually made from cast iron or steel and can be found in two different shapes; single-sided and double-sided. A single-sided drum has one side that houses the friction material while the other side remains empty. This allows it to rotate freely when used as a wheel. The double-sided type has both sides covered with friction material and will not be able to rotate if used as a wheel.
The shoe is the part that makes contact with the drum when stopping, it is usually made from cast iron or steel but can also be rubber. The shoes are designed so that they can be replaced easily when worn out or damaged; this makes them more cost-effective than disc brakes which require the replacement of the entire brake system. Some drum brakes have a third shoe called the “spool” which is attached to the wheel and provide additional friction when stopping.
The spool has a long shaft that connects it to the rest of the brake system; this shaft is usually round with threads on both ends so that it can be rotated into different positions depending on how much force needs to be applied.
To apply pressure to the drum, there are two types of systems: direct and indirect. In a direct system, the wheel itself acts as part of the braking system by applying pressure on the friction material inside the drum. In an indirect system, a separate mechanism is used to apply pressure on the friction material; this can be done using either a brake shoe or the spool itself. A direct system uses more force than an indirect one and has less wear on its parts; it also creates better-stopping power because there are no other moving parts that can fail in an indirect system.
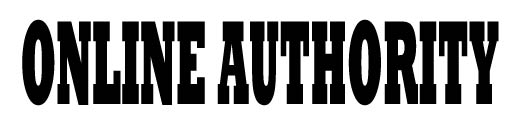