Industry
How to Streamline Your Manufacturing Process
Efficiency is paramount for managing a warehouse or a small production plant. The optimal scenario is to use as little handling by staff to get the most work done. Every project manager working within delivery deadlines knows this. One obvious choice, given the level of technological advancements, is to automate whenever possible. Machines don’t take days off unless they need servicing, they produce more consistent output and if designed properly, they operate safely. However, putting this disruptive concept into practice creates a lot of issues.
So we are stuck with a sort of a hybrid model where automation takes care of certain tasks while your warehouse workforce does the rest. Or the other way around. Whatever the case, the struggle for streamlining your production process (or material handling of warehouse stockpiles) is real.
You need to find a way so that your workforce puts their work where it matters the most. And keep your automated machines running efficiently against cost constraints.
Automated Position Control
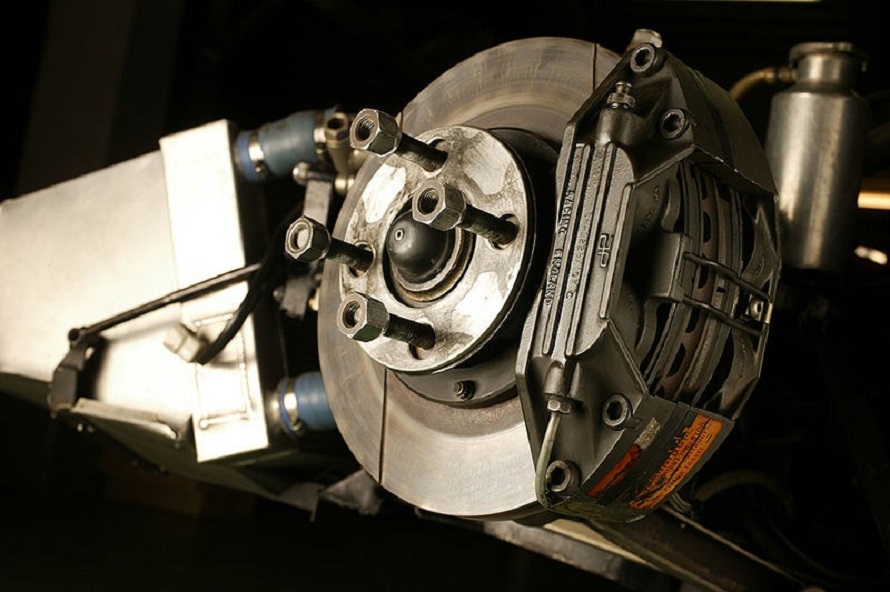
In many industries, the production sequence simply has to be synchronized. The most prominent example is mechanical engineering, however, the petrochemical industry, mining and many others require reliable position control too. Because of this, high-quality industrial brakes and clutches have become a very important part of the production line.
They usually come in pairs. Clutches mostly serve as a bridge between moving machine sections and brakes stop elements in place. So if the process requires rapid deceleration and controlled positioning you will benefit from introducing brakes and clutches. It’s a sort of a trend to replace existing hydraulics along the production line with electromagnetically operated braking machines. The latter are more efficient, require less servicing, and are safer to operate.
Electric spring-applied brakes stop masses in motion across industries. They are used in cranes, the food processing business, and textile machines. Electromagnetically released spring-applied brakes are used wherever masses in motion have to be decelerated as quickly as possible or where masses must be held in a defined position.
Modern application of friction materials significantly increased the use of clutches. These advancements ensure consistent coefficients of friction and are more durable in the long run. So what is the best clutch material? Organic, ceramic, kevlar, feramic, and similar materials are used to make them. But assigning one of them as best is a tough call simply because they cover diverse industries that can’t be compared.
How can we compare phenolic resins, fiberglass, and metallic powders, with silicon, steel, graphite, or compounded rubber? We can’t and you would need to take into consideration the specific production process before choosing a brake and clutch system.
Signaling Equipment
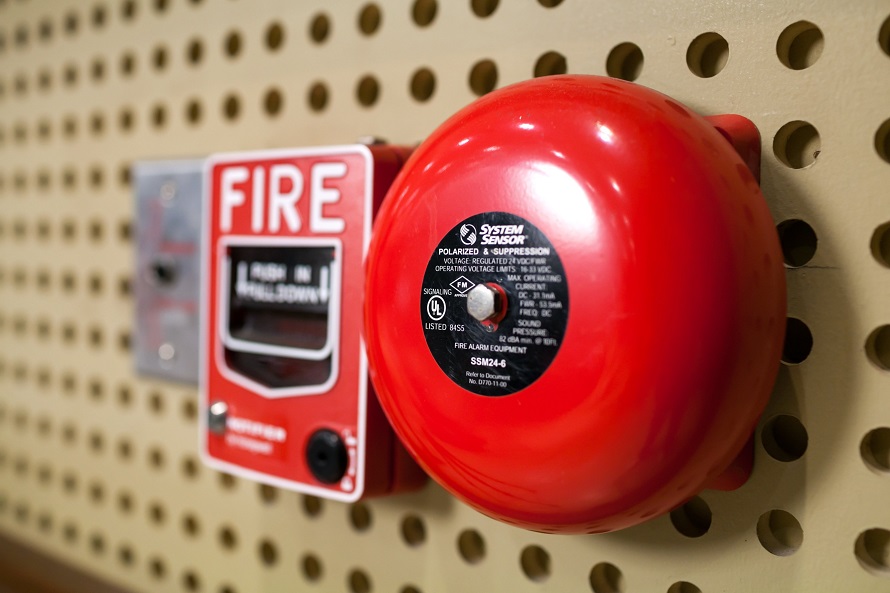
Integrating warehouse processing methods can be a pain. Especially if you need to also consider safety regulations and standards. Workforce safety is often placed at the bottom of the list of priorities, although there are reasons to fundamentally change this. Primarily because the company needs protection against lawsuits from their employees.
Accidents and safety incidents bring morale down – this will affect your usual streamlined efficiency. And if an incident leads to interruption of your regular operations, there will be hell to pay when the music stops.
So, better invest in production plant safety before you are forced to sort out human resources and public relations nightmare. Set up stack lights to indicate the status of the production sequence so that your workforce can be safe. Rotating lights and beacons can do this too. These types of visual aids are great for noisy environments.
If audible sounds can be easily perceived then you can go with loudspeakers, buzzers, horns, alarms, and sirens. They can be used in all phases of a typical warehouse activity, the way a regular car emits sounds when moving in reverse. Don’t forget safety eventually translates into efficiency.
Packing and Shipping
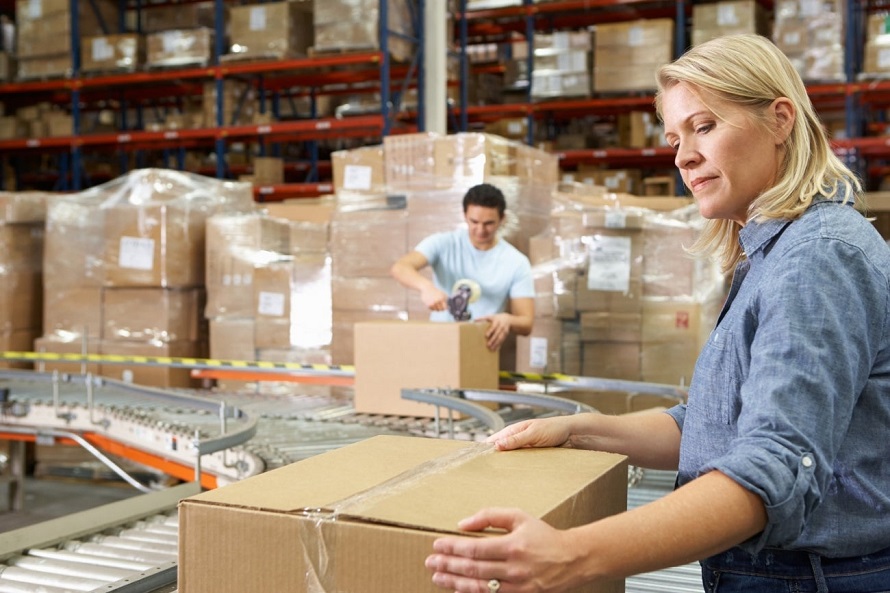
Clients have grown accustomed to top-notch packaging of finished products. Marketing teams have invested efforts to make presentation or unboxing an experience, rather than a straightforward delivery of a plain object. This is more typical for small-sized products.
On the other hand, bulky, sizable, and fragile products require safe enclosure on their way along the supply chain. You have to protect a product that got through quality testing (and many hours of work) before you send it off to your clients.
Then again, not everything that comes out of a stockpile has the same measurement. So, going for adjustable carton sealing machines is very prudent. Electrically powered automatic packaging sets run on the typical current draw (220V/50Hz, 400W). Some carton sealers boast a speed of up to 30 cartons in a minute. And when you need to go to the next item you can easily modify the length of the package. Width and height are limited (120-480mm) but cover a wide array of products that can be put into such boxes.
Technically advanced carton sealing machines are durable and have a long service life. This is particularly so with the robust, heavy-duty sealers which can be operated at worktable height. They are portable (on wheels) and easy to use.
This is not where efficiency stops though. If you deal with wholesale orders then you can also benefit from adding a pallet wrapping machine to your process. It surely does help keep shipping costs at a minimum, especially when sending stuff overseas.
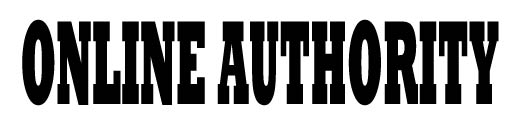